Everything You Need To Know About Cut-Resistant Glove Levels
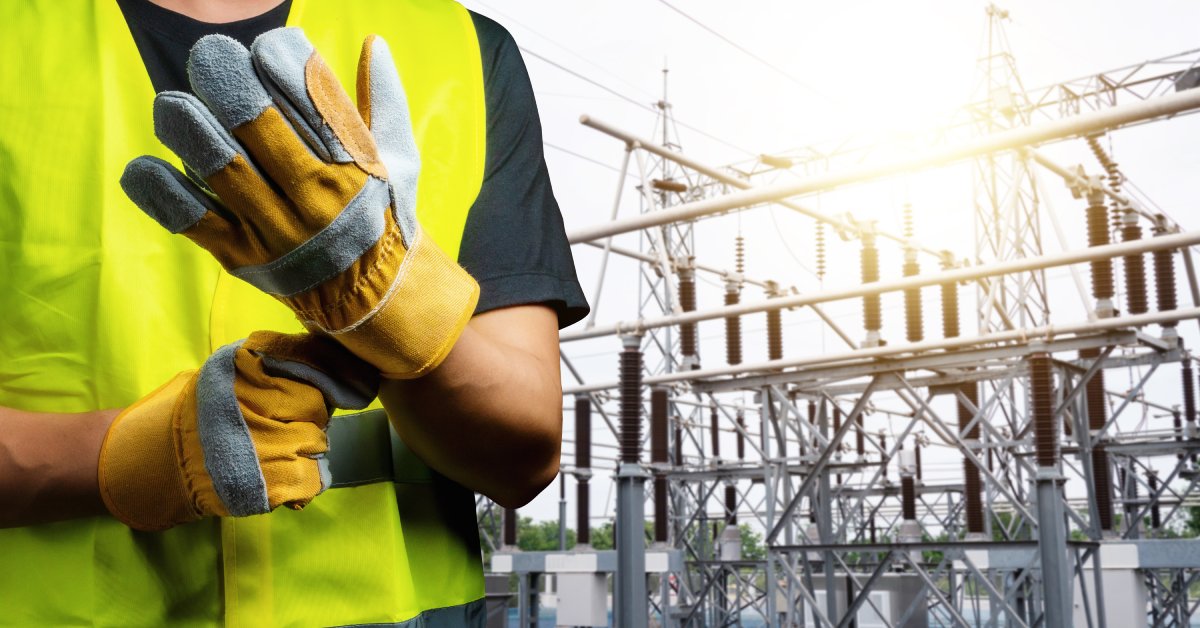
Cut-resistant gloves are essential pieces of protective equipment for industries ranging from food preparation to construction. They shield your hands from injuries caused by sharp objects and tools. But how do you determine which gloves match your specific needs? The answer lies in understanding their cut-resistance levels. Each level corresponds to a specific strength, governed by testing and safety standards. Let’s break down everything you need to know about cut-resistant glove levels.
What Are Cut-Resistant Gloves, and Why Are They Essential?
Cut-resistant gloves shield your hands from cuts, abrasions, and punctures using high-performance materials such as Kevlar, high-performance polyethylene (HPPE), and metal mesh. These materials create a protective barrier while maintaining flexibility, allowing you to work safely without sacrificing precision.
Certain industries require cut-resistant gloves due to the risks workers face daily. Food processing businesses rely on these gloves to protect employees during repetitive cutting with sharp knives. Construction and metalworking industries enforce their use because workers consistently handle jagged materials like glass or sheet metal.
The Occupational Safety and Health Administration (OSHA) and other safety organizations demand protective gloves to reduce workplace injuries and maintain compliance.
Cut-Resistance Standards
Standards in North America provide clear guidelines for determining protection levels, ensuring safety across industries in the United States and Canada. In particular,The American National Standards Institute (ANSI) sets the benchmark for cut-resistant gloves.
ANSI measures cut resistance using levels labeled A1 through A9. Lower levels, such as A1 and A2, provide basic protection for tasks involving minimal risk, such as food preparation or handling small tools. Mid-level ratings, A3 to A5, suit jobs requiring moderate protection, such as assembling machinery or working with sheet metal. For the most hazardous environments, gloves rated A6 to A9 deliver maximum resistance and are ideal for tasks such as glass installation or steel handling.
Testing Method
Testing evaluates how much force a glove’s material can endure before a blade cuts through it. During a test, technicians place the glove material securely on a machine. The blade moves across the material under controlled pressure, replicating real-world cutting conditions.
The machine records the exact force, measured in grams, required to penetrate the glove. For example, an A1-rated glove resists lower force, while an A9 glove withstands much stronger pressure. Technicians calibrate every variable, including blade sharpness, speed, and material tension, to keep results consistent. This process accounts for features such as coated palms or reinforced layers, ensuring all glove designs have accurate ratings.
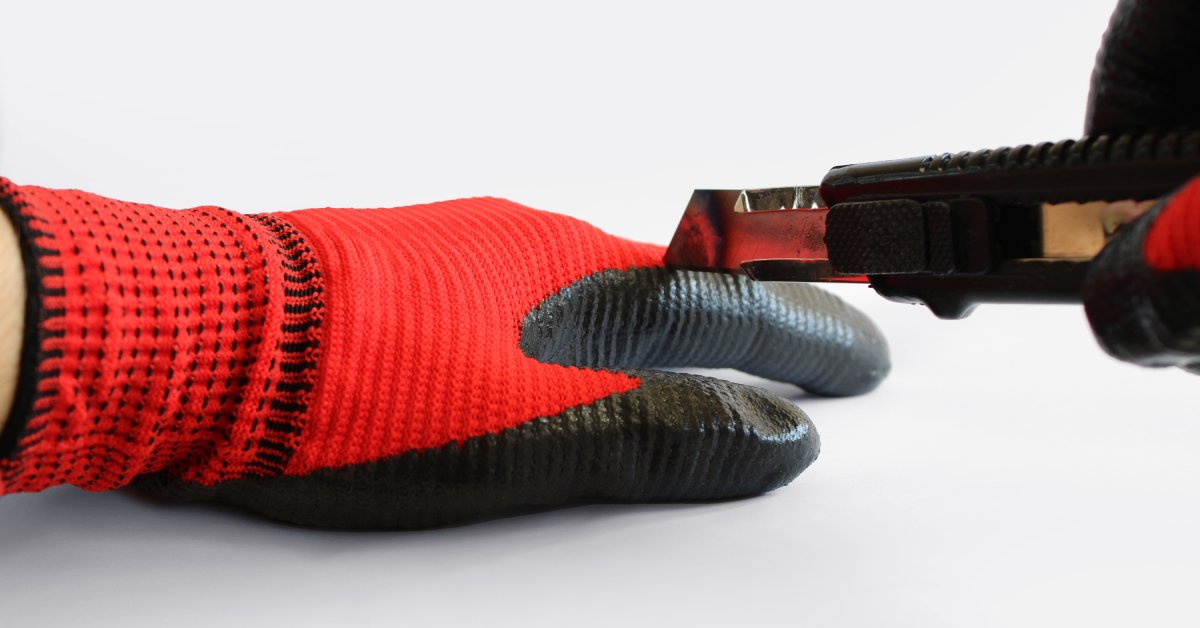
Understanding Protection Levels Across Industries
The most important thing you need to know about cut-resistant glove levels is that the level you need depends on your industry’s specific hazards and tasks. You can pinpoint the best option for your work environment for learning the ANSI categories.
Low Protection Levels for Light Tasks
ANSI A1 and A2 gloves suit tasks with minimal risks, providing basic protection without sacrificing comfort or flexibility. Workers in food preparation, such as chefs or line cooks, benefit from these gloves to prevent minor nicks when slicing fruits or vegetables.
Packaging handlers or warehouse employees opening cardboard boxes also find these gloves useful for avoiding small cuts from paper or lightweight tools. Most A1 or A2 gloves are lightweight, breathable, and ideal for extended use.
Mid-Level Protection for Moderate Risks
ANSI A3 to A5 gloves support jobs with moderate cut risks. For instance, auto mechanics rely on these ratings when replacing parts such as brake components or working around sharp edges in engine assemblies.
Manufacturing workers assembling small machinery or handling precut metal sheets also require middle-tier protection. The gloves balance cut resistance with dexterity, allowing workers to handle detailed or precise tasks without losing a strong sense of touch.
Some designs feature coated palms for enhanced grip, which can improve safety when handling slippery or oily materials.
High-Protection Gloves for Heavy-Duty Tasks
Industries including construction, glass production, and metal fabrication demand the maximum protection provided by ANSI levels A6 to A9. Workers installing glass panels need these gloves to shield their hands from deep cuts caused by jagged edges.
Similarly, laborers in steel construction or shipbuilding use high-protection gloves to handle sharp beams or cables. Recycling jobs, such as waste sorting, where you constantly encounter broken glass or twisted metal, also require this caliber of hand protection.
These gloves typically incorporate multiple layers of high-performance materials such as Kevlar or HPPE, ensuring durable protection in extreme, high-risk scenarios.
Tips for Properly Using Cut-Resistant Gloves
Using cut-resistant gloves correctly ensures you get the maximum protection they offer. When buying a new pair of gloves, ensure a proper fit. Loose gloves can slip off or snag on equipment, while tight gloves restrict movement. Select a pair that fits snugly but allows for comfortable hand movement.
Inspect your gloves for wear and tear before each use. Replace damaged gloves immediately, as they compromise protection and increase injury risk.When wearing your gloves, avoid applying extreme pressure or executing stabbing motions that could exceed the glove’s protective capabilities.
Addressing Common Myths Around Cut-Resistant Gloves
Misunderstandings about cut-resistant gloves can lead to improper use or false expectations, putting workers at risk. Clearing up these myths helps you make smarter decisions.
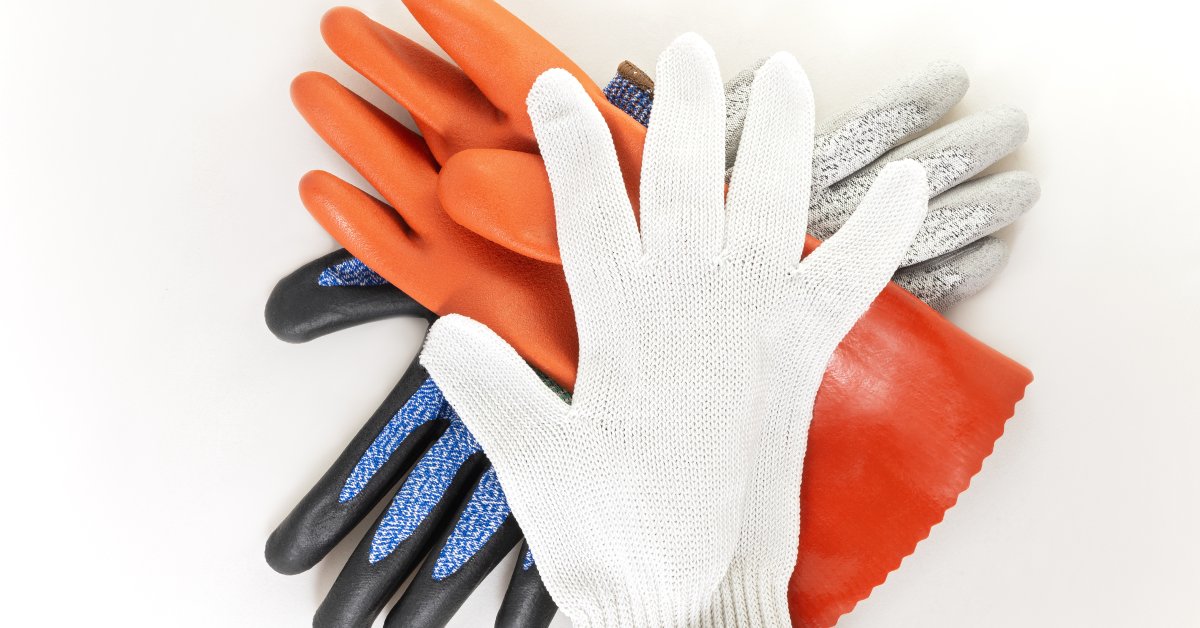
“All Cut-Resistant Gloves Are Cut-Proof”
Cut-resistant gloves reduce injuries, but they don’t eliminate risks altogether. Even high-rated gloves like ANSI A9 can fail under extreme force or sharp stabbing motions. For instance, while PIP MaxiFlex Cut gloves effectively protect against slicing accidents during everyday tasks, no material can withstand direct stabs from a high-powered blade. Combining these gloves with proper tool-handling practices ensures the highest level of safety.
“Higher Ratings Always Mean Better Gloves”
Choosing gloves with the highest cut-resistance rating doesn’t guarantee they’re the best fit for your job. Different tasks require different levels of protection. For example, if you work in assembly lines handling small, precise components, the PIP G-Tek PolyKor gloves strike the perfect balance between dexterity and moderate cut resistance.
Meanwhile, tasks involving more significant hazards, such as dealing with sharp glass or metal edges, align better with gloves rated for higher protection, such as the PIP Scrap King gloves. Always match the glove’s level and design to the task to maximize both safety and performance.
“There’s No Difference Across Brands”
Not all gloves offer the same quality, even if they show comparable resistance levels. Some brands incorporate advanced features, offering superior comfort, durability, or specialized coatings. For instance, PIP MaxiFlex Ultimate gloves stand out for their nitrile coating that enhances grip. Similarly, the G-Tek PolyKor line includes innovative materials that combine lightweight designs with excellent cut resistance.
Equip yourself with the right gloves by exploring trusted brands, such as PIP MaxiFlex and G-Tek, at H-To-O Supply today!
Recent Comments